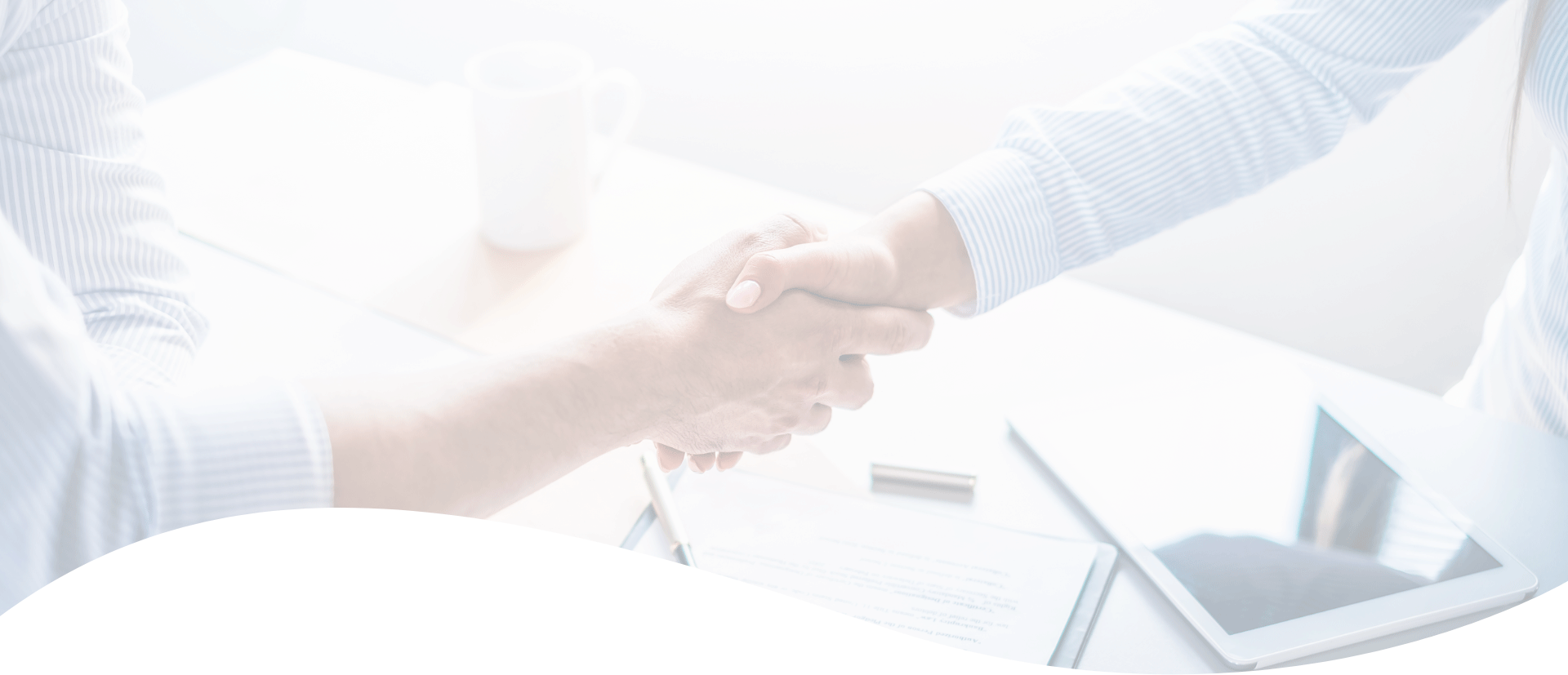
Services
Process Equipment Services & Support
Liquidyne’s emphasis on customer success is the driving force behind our Process Equipment Services and Support. With over three decades of industry experience our team has the expertise and knowledge needed to enhance operational excellence. Our process equipment services and support encompass our custom engineering and fabrication program providing both multi-use equipment and single-use assemblies, built in our Certified ISO 14644 Class 7 Cleanroom. We also provide a range of on-site services including equipment audits and inventory management.
Single-Use Solutions
Liquidyne specializes in designing and implementing single-use technology solutions to the Biotech and Pharmaceutical industries with an emphasis on "Performance with Value". We utilize our ISO 9001:2015 Certified Quality Management System to ensure consistency and reliability with every SUA solution we deliver, we call it "Process Perfected".
Cleanroom
Custom single-use and stainless steel products, assemblies and equipment are manufactured in Liquidyne’s Certified ISO 14644 Class 7 Cleanroom. Our cleanroom is a combination of an ISO 8 transfer area and an ISO 7 area for production. Products fabricated in our cleanroom are sterilized and validated, supporting our customers’ need for highly controlled, documented manufacturing of custom assemblies.
Crib Management
Keeping production running smoothly requires having a consistent stock of process equipment and components. In order to facilitate easier inventory management for our customers, Liquidyne offers inventory, or crib, management services. Our trained team assists with setting up, monitoring, and refilling back-inventory in order to ensure reduced downtime and enhanced operations.
Custom Fabrication
Liquidyne’s team of industry experts and engineers can create and customize solutions to meet a variety of customer needs. Our ISO 9001:2015 certified facility produces custom carts and assemblies which meet or exceed regulatory and industry standards for sanitary equipment. Custom fabrication products include pump carts, filtration integrity testing carts and sanitary hose assemblies.
Process Audit
Liquidyne’s team of industry experts and talented process engineers provide manufacturing process equipment audits. During a site visit, our team evaluates current processes for outstanding issues such as voided warranties, safety concerns or maintenance problems. When appropriate, equipment audits may also include suggestions for changing the existing setup using alternate or improved product choices.
Service & Support
Liquidyne is proud of our customer-first approach to service and sales. We partner with industry-leading manufacturers to bring high-quality products to our customers. In addition to our role as a supplier we also provide services, such as process design, audits, and support, including inventory management and ongoing maintenance programs. Our 3 decades of industry expertise guide us as we work with our customers to provide solutions to their most complex problems.
At Liquidyne, we prioritize our commitment to quality and consistency. In 2017 we achieved ISO 9001:2015 Quality Management System certification to ensure we can repeatedly deliver consistently high-quality products and solutions. Being ISO 9001:2015 QMS Certified by Amtivo (USA), Inc, together with our USP Class VI Testing, ASME Bioprocessing Equipment (BPE), and EHEDG certification guarantee, we have the methodologies to assure quality. We will quickly and accurately rectify any issues if any of our products are ever in non-conformance.